This is the English translation of the Interview with Pavel Bolf, swordsmith from Czech Republic. The original article is in Czech language ( čeština ) in the issue number 13 of the magazine.
We keep asking questions and trying to grasp the meaning and the magic of traditional craftsmanship. This time, we spoke with Pavel Bolf – a well known swordsmith from Czech Republic – about Japanese blades, quality, tradition, and creativity in crafts. Pavel makes amazing swords and knives. It is his passion – and profession.
EN: What brought you into sword smithing? And how did you know it’s your real passion and profession?
EN: I have been interested in cold weapons since elementary school. I learned about Japanese swords in TV series like “Shogun” and “Falcon, guardian of the night”. I also started studying martial arts at that time. This naturally created the need to own a katana. However, in the days of the communist regime in Czechoslovakia, it was not possible to buy a sword. So, I decided to make one. I made my first attempt while studying in high school. Then later, I tried a couple more times. At that time, my knowledge of the field was not even below average. It wasn’t until the year 2000 that I started studying and producing swords seriously. That’s when I decided that sword making would become my livelihood.
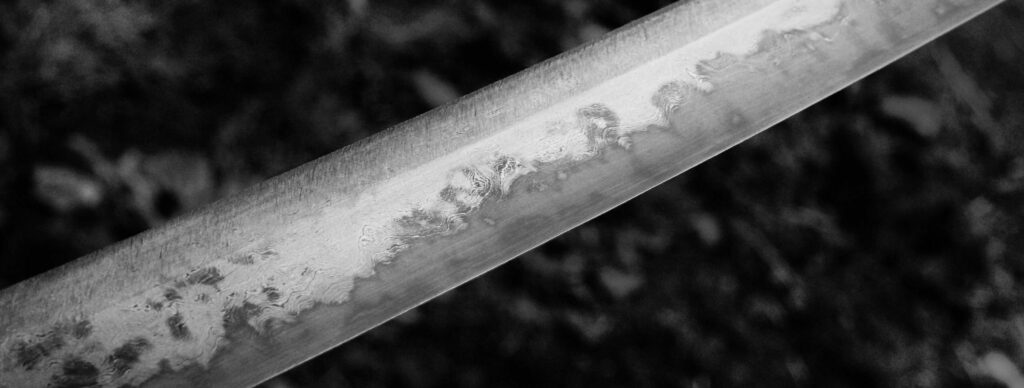
EN: On your website it says, “traditional Japanese sword making”. What makes it “traditional”?
EN: This is an interesting and important question. When I started making Japanese swords, their blades were forged from homogeneous modern steel. Later, I started layering the same steel by folding it. However, none of these are real Japanese swords. For a traditional sword, the starting material is key, which is steel, reduced in the Tatara furnace on charcoal. This method produces steel of a specific type and character. Its properties will then be reflected in the finished blade.
The type and composition of the iron ore you use to make traditional Tamahagane steel are also important. It is magnetite in the form of sand (Satetsu) of maximum chemical purity. Thus, it does not contain elements such as sulfur, phosphorus, and others, which are a common part of iron ore mined in Europe. Steel produced in this way is cleaned, homogenized and its carbon content is reduced to the required quality. This process is time-consuming and demands advanced techniques. It requires a lot of experience. The next important step is hardening. With Japanese swords, only the blade is hardened. This creates a temper line, which is one factor in evaluating blade qualities. That’s about the topic of traditional blade making in a nutshell. However, it is similar in the next steps, polishing the blade and making the kit. It is necessary to use original processes and authentic materials.
EN: How did you learn the craft?
EN: I’m basically self-taught. Before the mass spread of the Internet, there was little information. I verified a lot of information in a “trial/error” style. However, this method proved to be a good way of verifying information even for the present. Today, there is a lot of information, and it is difficult to select the valuable, true ones from assumptions and half-truths. After the year 2000 I began visiting Japan regularly. I never got to study sword making with a Japanese blacksmith, which has turned out to be an advantage over time. I am much more open to information from other sources. Less prone to accept dogma. To me, swordsmanship is a craft, not a religion. In Japan I mainly study old swords. Their metallurgy. Then at home I try to discover the technological processes by which these metallurgical qualities were achieved. 90% of my study is practice.
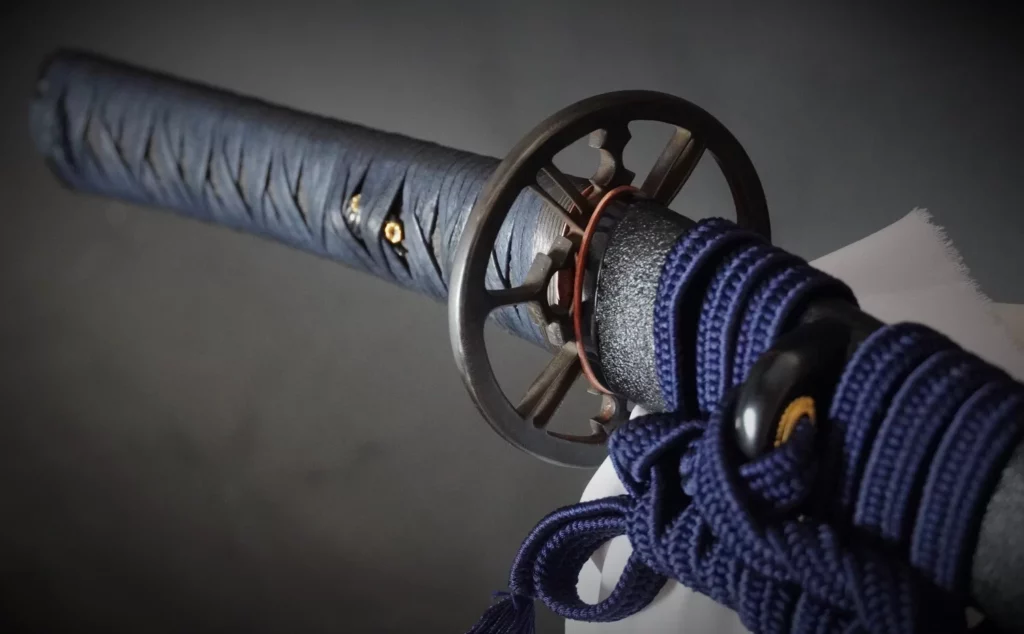
EN: You refer to different Japanese schools of sword making. What is the difference between those schools?
EN: In the beginning there were 5 schools in Japan (gokaden). Later, others were created from them. The production of steel and swords was not centralised, or centrally controlled. Small differences in the local raw materials used and in the crafting approach also had an effect on the shape of the swords. They differed in the details of construction (shapes), in the structure of the folded steel, in the way of combining different types of steel, in the hardening style and in the hamon line. Nowadays, an expert in kantei (sword evaluation and recognition) is able to match these details to an antique blade to a period, a school, and often to a specific swordsman.
EN: Who is buying Japanese swords these days and why?
EN: In the first half of my career as a swordsmith, my swords were bought almost exclusively by people practicing martial arts. At the time when the quality and authenticity of my work began to be of interest to collectors of old swords, they also began to buy them. And people studying Japanese swords. Today, some customers also buy them as an investment. Someone is just having fun and fulfilling a warrior’s dream.
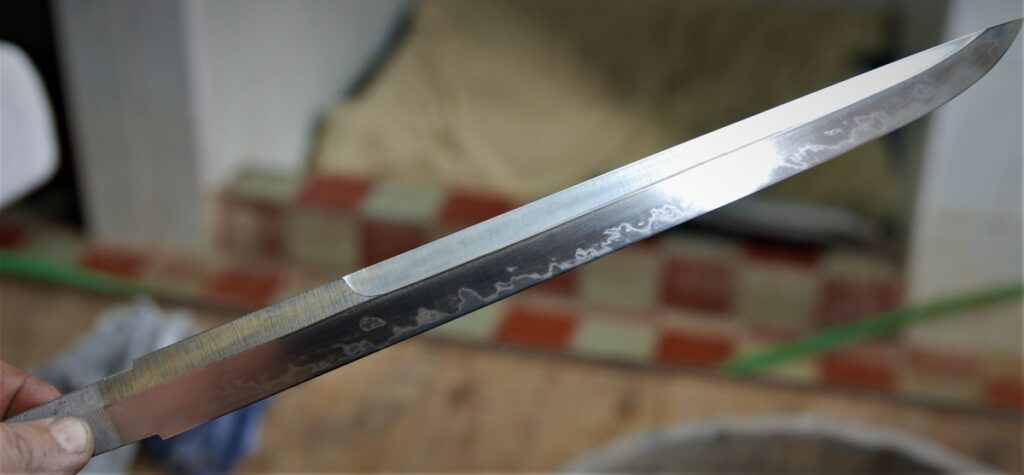
EN: What defines “quality” in a sword or a knife? (In other words, how would you describe the difference between a good quality product and bad quality?)
EN: Swords and knives should, of course, be sharp, with a durable edge. Able to cut and perform its function. The topic of the “sword as a weapon” is essentially a taboo in Japan today. They consider it more of an art object. This can lead to a loss of function. This exaggerated artistic influence was manifested in swords in the Edo period (after 1600) when warfare ceased in Japan. Some swordsmanship styles began to focus on artistic workmanship. This also changed the techniques, especially the tempering process. Some swords thus became fragile ornaments that were incapable of real combat stress. They broke. Of course, both the knife and the sword can be beautiful. Beauty and functionality should be balanced. Then there is metallurgy. Old swords, especially swords produced in the 12th-14th centuries, are extremely rich and interesting metallurgically. This was largely lost in the Edo period. Many swordsmiths today with the metallurgical qualities of the old swords are trying to get closer, but they are unable to do so. The reason is probably the low sensitivity of the Tamahagane steel used and the heat treatment techniques used. These correspond to the techniques created in the Edo period. It took me several years before I figured out ways to make blades with authentic metallurgy. I am still researching and improving this issue.
EN: In one of the documentaries on your website, you said what you do is “amateur, far away from what they do in Japan”. What do you mean? What are they doing differently in Japan?
EN: I’m a swordsmith. I make steel and use it for blades. I consider myself a successful professional in this field. But then there are the other fields. Polishing, production of wooden parts of the kit, production of metal parts, painting, braiding of the handle. Each field in Japan is performed by a specialist. And even within a specialization, they often only produce products of certain styles or schools. That’s why the final product, a sword assembled from expertly crafted parts, is so perfect. I am able to make a complete sword. However, it is impossible for them to master all fields and trades at a top level. So I’m a specialist in blades, and I also make very good sword guards. Polishing or accessories, I can do those at a decent-average level, but not pristine. My wife has been polishing for the last 10 years. She’s getting pretty good at it. Better than me. But it must also be said that there is a price to pay for top Japanese quality. The Japanese prices of specialised craftsmen are several times higher than the prices of my “amateur” but authentic and well-crafted components.
EN: The fittings and housings of the sword (tsuka, koshirae…?) are fascinating! Are there strict rules, or it’s a place for creativity of the master?
EN: This is a very broad topic. As I mentioned, this is the work of specialised professionals. Similar to blades, there are many styles, schools, period differences. Everything has its strict rules. My personal opinion is probably like this. For the first five years, a craftsman learns the basics. Hard intensive study and practice. No personal input, just repeating and copying the teacher. For the next five years, he learns to use the basics and improve the technique; still studying and practising, without personal striving for style. The next five years are already at a good craft level. Heworks independently, improves his skills. At the end of this period, he begins to understand the essence of the craft. And then he can start creating his own style. However, the rules, shapes, and specific details of individual styles are given. The best has already been created. Rather than creativity, style is shaped by the quality and distinctiveness of its craft. A craftsman often creates his own high-end works at the end of his career. Not everyone can do it. Most adepts don’t last the first five years. It is easier to make knives. There is a lot of room for your own creativity and ego.
Interview by Natasha NawaTaNeko / Editing and translating: Noirot